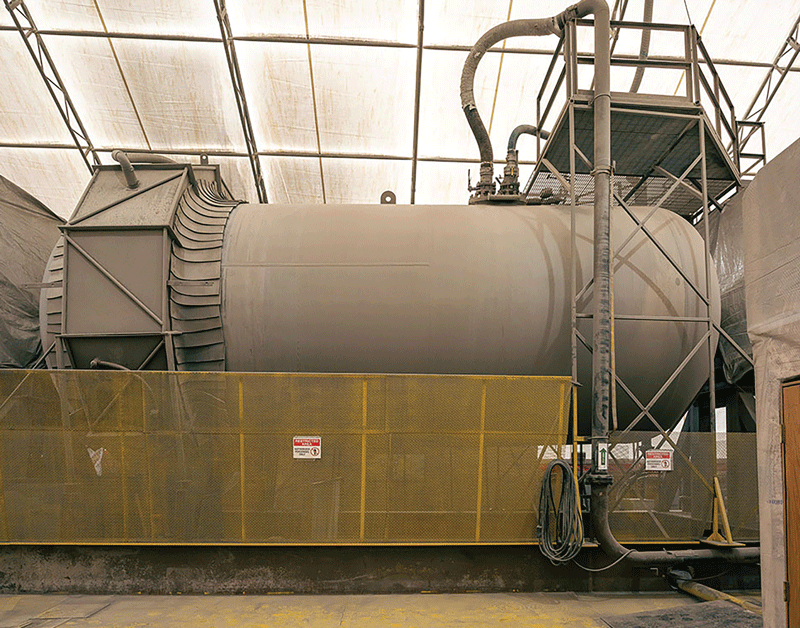
An Industry Strategy for Limiting Carbon Emissions
By Alfredo Carrato
When it comes to limiting the amount of carbon emissions globally responsible for advancing climate change, the construction sector has a substantial role to play. Overall, construction is responsible for more than one-tenth of total carbon emissions around the world, and a large portion of this carbon footprint comes from the manufacturing of building materials such as cement, the second-most consumed material in the world after water.
However, the past decade or so has seen significant advancements in methodologies for reducing carbon emissions in the cement production process. One of the most promising and rapidly growing methodologies is called Carbon Capture, Utilization, and Storage (CCUS), representing a suite of technologies designed to prevent the carbon dioxide that manufacturing processes produce from going into the atmosphere.
Several leading organizations, such as the International Energy Agency, the International Renewable Energy Agency, and the Intergovernmental Panel on Climate Change, have released long-term initiatives that rely on the expansion of CCUS to limit the global temperature rise to just 1.5 degrees Celsius. The IEA has also cited CCUS among the most cost-effective options for the decarbonization of carbon-heavy industries, many of which operate across the construction value chain.
Before outlining the specific CCUS methodologies that are gaining real momentum today, it’s important to clarify exactly how it works and the various ways it promises to lower the carbon impact of cement production.
What is CCUS?
Carbon emissions are an unavoidable byproduct of traditional cement production. This is because a core component of Portland cement – the most widely used cement today – is limestone. When this mineral is heated, the carbon trapped inside the limestone is usually released.
CCUS allows cement manufacturers to capture this carbon byproduct from points of emission within the manufacturing facilities or directly from the air. Such captured emissions can then be safely stored underground in geological formations, injected into concrete to strengthen it, or used to make other valuable products.
Companies leveraging CCUS
Though CCUS has only gained widespread attention fairly recently, the technology has been achieving real results for several decades. In 1996, the first large-scale CCS project was commissioned at the Sleipner offshore gas facility in Norway. At Sleipner and Snøhvit, another leading project in Norway, over 20 million tons of CO2 have been safely stored to date.
Today, more than 30 cement CCUS projects are in different development stages worldwide, the majority of which are based in Europe. In the United States, the U.S. Department of Energy is currently conducting feasibility studies for multiple projects in California, Colorado, Texas, Missouri and Indiana, among others. However, much of the CCUS progress worldwide is taking place at the startup level, often thanks to collaborations with sustainability-focused venture capital firms.
In England, a startup called Carbon Clean has developed proprietary technology that captures carbon emissions from the flue gas that gets released through a cement plant’s smokestack. The technology is currently in use at cement facilities in several countries such as India and more recently Germany, where the goal is to standardize carbon capture and achieve cost-competitive carbon neutrality across so-called hard to abate industries before 2030.
This is just one of the myriad CCUS-related startups that has garnered considerable venture funding as of late, which reflects the increasing prioritization of sustainability in the global construction sector.
Challenges for CCUS
The biggest drawbacks to CCUS are the high upfront capital costs for the equipment to separate the carbon, the high energy costs of keeping the equipment running, and the costs related to transportation and safe storage of the captured CO2. According to a recent report from the U.S. Department of Energy, to cover these expenses a cement manufacturing organization would need to spend another $22 to $55 for every metric ton of cement produced.
Alfredo Carrato is a trained architect, BIM enthusiast and college professor who scouts for breakthrough decarbonization technologies for the construction industry. As an Investment and Open Innovation Advisor, he oversees investment activities and partnerships at Cemex Ventures, with a focus on tackling the carbon footprint challenge of the construction sector.
SUBSCRIBE TO THE DIGITAL OR PRINT ISSUE OF SABMAGAZINE FOR THE FULL VERSION OF THIS ARTICLE.